Product performance introduction
In the demanding environment of chemical processing facilities, flooring systems must meet rigorous standards in terms of durability, safety, chemical resistance, and ease of maintenance. Traditional materials such as steel and aluminum often fall short in highly corrosive settings. Fiberglass grating, also known as FRP (Fiberglass Reinforced Plastic) grating, has emerged as the optimal solution for industrial flooring in chemical plants due to its exceptional performance and cost-effectiveness over time.
Superior Corrosion Resistance
One of the primary reasons fiberglass grating is widely used in chemical plants is its outstanding resistance to corrosive chemicals, acids, alkalis, and solvents. Unlike metal grating, which can corrode, rust, or deteriorate quickly when exposed to aggressive substances, FRP grating is engineered to withstand harsh chemical environments. Depending on the resin used — such as vinyl ester, isophthalic, or phenolic resin — fiberglass grating can provide tailored protection against specific chemical exposures. This makes it suitable for use in areas such as mixing stations, tank farms, acid recovery zones, and waste treatment systems.
Enhanced Safety and Anti-Slip Performance
Safety is a top priority in any industrial facility. Fiberglass grating features anti-slip surfaces such as gritted or concave finishes, which provide excellent traction even when wet or contaminated with chemical residues. This significantly reduces the risk of slips and falls, protecting workers in areas where spills and splashes are common. Furthermore, FRP grating is non-conductive and spark-resistant, adding another layer of safety in electrical and flammable chemical processing zones.
Strength and Load-Bearing Capacity
Despite being lightweight, fiberglass grating offers impressive load-bearing capabilities. It can be used for flooring, walkways, stair treads, trench covers, and platforms in areas with moderate to heavy foot traffic or equipment loads. Pultruded FRP grating, in particular, is ideal for applications requiring high mechanical strength over long spans.
Low Maintenance and Long Service Life
In chemical plants where downtime is costly, minimizing maintenance is critical. Fiberglass grating is virtually maintenance-free. It does not require painting, coating, or galvanizing. Its non-corrosive nature prevents degradation, and its non-porous surface resists staining and microbial growth. With proper installation, FRP grating can last 20–25 years or more, reducing the total cost of ownership.
Easy Installation and Fabrication
Thanks to its light weight — approximately one-third the weight of steel — fiberglass grating is easy to handle, transport, and install. It can be cut on-site using standard carbide tools, which eliminates the need for hot work permits or special equipment. This simplifies retrofitting and customization in complex plant layouts.
FRP Grating Specifications & Technical Parameters
1. General Specifications
Item | Description |
---|---|
Product Type | Molded FRP Grating / Pultruded FRP Grating |
Mesh Size | 38×38 mm (1.5″x1.5″) / 40×40 mm / Custom |
Thickness (Height) | 25 mm / 30 mm / 38 mm / 50 mm |
Panel Size | 1220×3660 mm / 1000×4000 mm / Custom |
Open Area | 60% – 70% (depending on mesh size) |
Surface Options | Gritted / Concave / Smooth / Covered Top |
Color | Gray, Yellow, Green, Red, Custom |
2. Mechanical Properties (Typical Values)
Property | Value | Test Standard |
---|---|---|
Tensile Strength | ≥ 120 MPa (17,400 psi) | ASTM D638 |
Flexural Strength | ≥ 200 MPa (29,000 psi) | ASTM D790 |
Flexural Modulus | ≥ 7,800 MPa (1.13×10⁶ psi) | ASTM D790 |
Compressive Strength | ≥ 200 MPa (29,000 psi) | ASTM D695 |
Impact Strength (Izod) | ≥ 85 J/m | ASTM D256 |
Barcol Hardness | ≥ 40 | ASTM D2583 |
3. Physical & Chemical Properties
Property | Value | Test Standard |
---|---|---|
Density | ~1.8–2.0 g/cm³ | ASTM D792 |
Water Absorption | < 0.5% | ASTM D570 |
Flame Retardancy | ≤ 25 (Class 1) | ASTM E84 |
UV Resistance | Available with UV inhibitor | – |
Electrical Conductivity | Non-Conductive | – |
Thermal Conductivity | ~0.25 W/m·K | ASTM C177 |
Operating Temperature Range | -50°C to +120°C (varies by resin) | – |
4. Resin Systems Available
Resin Type | Features | Application Areas |
---|---|---|
Orthophthalic | General purpose, cost-effective | General industry, flooring |
Isophthalic | Improved chemical resistance | Wastewater, food processing |
Vinyl Ester | Excellent chemical and corrosion resistance | Chemical plants, offshore, mining |
Phenolic | Fire and smoke resistance | Oil & gas, transport, marine |
5. Load Table (Example for 38mm Thick Grating)
Span (mm) | Load (kN/m²) | Deflection (mm) |
---|---|---|
600 | 5.0 | 4.5 |
800 | 3.5 | 5.9 |
1000 | 2.0 | 7.6 |
Why Choose Us
Expertise in FRP Grating Manufacturing
With over 20 years of experience, our factory specializes exclusively in the design, development, and production of high-performance FRP (Fiberglass Reinforced Plastic) gratings. Our deep industry knowledge ensures that every product meets the most demanding industrial standards.
Advanced Technology and Equipment
We utilize state-of-the-art manufacturing equipment and precision molding technology to produce gratings with superior strength, corrosion resistance, and dimensional accuracy. Our commitment to innovation means your project benefits from the latest advancements in FRP technology.
Customized Solutions
From panel sizes and resin types to surface finishes and colors, we offer complete customization to meet your unique application needs—be it industrial flooring, stair treads, trench covers, or marine platforms.
Stringent Quality Control
Every product undergoes a rigorous quality inspection process, including load testing, flame retardance checks, and corrosion resistance analysis. Our ISO-certified quality management system ensures consistent excellence in every batch.
Competitive Pricing
We offer factory-direct pricing without compromising on quality. With optimized production processes and bulk manufacturing capabilities, we help our customers achieve cost savings at scale.
Reliable Delivery and Global Reach
We maintain a large stock of standard products and operate a streamlined logistics system, ensuring fast delivery times locally and internationally. We’ve successfully served clients in over 15 countries.
Hot-Selling Products
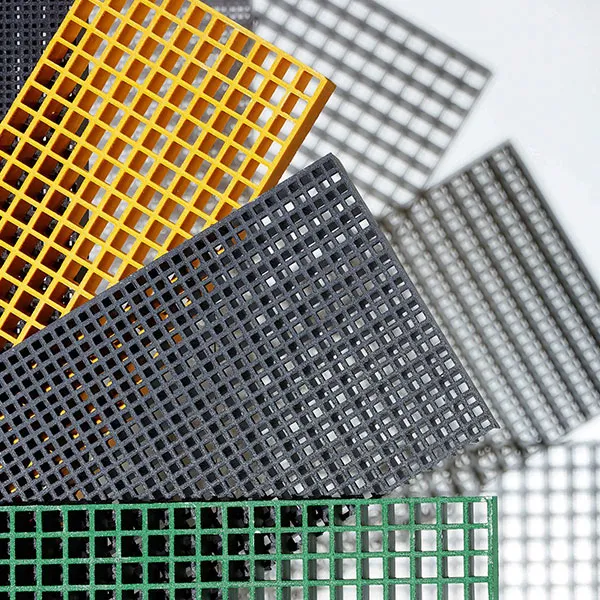
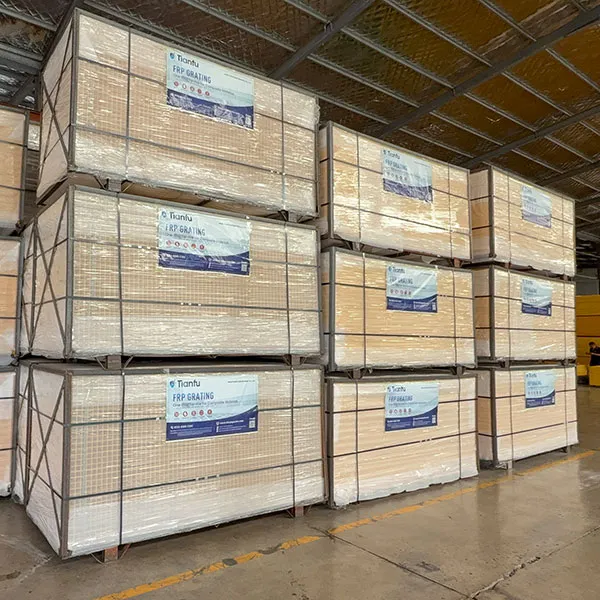

Standard Panel Sizes | 1220 mm × 3660 mm (4 ft × 12 ft) 1220 mm × 4000 mm (4 ft × 13.1 ft) 915 mm × 3050 mm (3 ft × 10 ft) 1000 mm × 3000 mm (customizable) (Other sizes can be customized according to project needs) |
Thickness Options | 25 mm (1 inch) 30 mm (1.2 inch) 38 mm (1.5 inch) — most common 50 mm (2 inch) |
Mesh Size (Opening Size) | 38 mm × 38 mm (1.5 inch × 1.5 inch) — Standard 40 mm × 40 mm 19 mm × 19 mm (mini-mesh for small object passage prevention) |
Load Bar Width and Spacing (for Pultruded Grating) | Load bar width: typically 25 mm, 38 mm, 50 mm Load bar spacing: 25 mm, 40 mm, 50 mm center-to-center |
Surface Options | Gritted surface (anti-slip) Smooth surface Covered surface (solid top) |
Colors Available | Yellow (most common) Green Grey Red Customized colors upon request |
Common Resin Types | Isophthalic Polyester (standard corrosion resistance) Vinyl Ester (high chemical resistance) Phenolic (fire-resistant applications) |
About the Factory
Anhui Tianfu New Material Co., Ltd is a leading professional manufacturer specializing in FRP moulded grating production. With over 20 years of experience in the composite materials industry, we are dedicated to delivering high-quality fiberglass reinforced plastic (FRP) solutions for a wide range of industrial and commercial applications. Our modern factory is equipped with advanced production lines, covering an area of more than 26,000 square meters. We offer a complete range of molded FRP gratings featuring superior strength, chemical resistance, fire retardancy, and anti-slip performance. At Tianfu New Material, we prioritize innovation, strict quality control, and customer satisfaction. Our products are certified to international standards and exported to over 30 countries worldwide, serving industries such as chemical plants, sewage treatment facilities, offshore platforms, and walkways. Whether you need standard sizes or customized solutions, Tianfu is your reliable partner for FRP moulded grating.
Application Scenarios
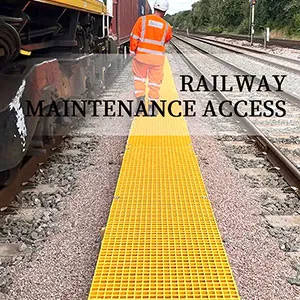
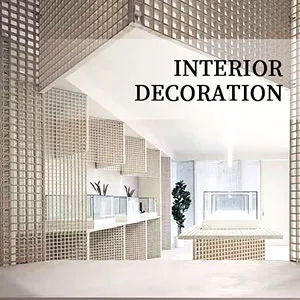
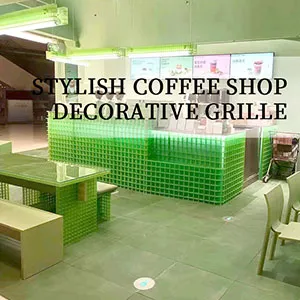
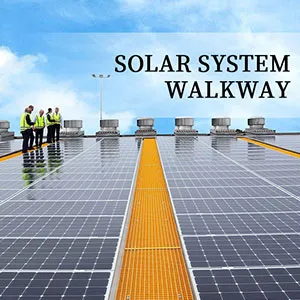
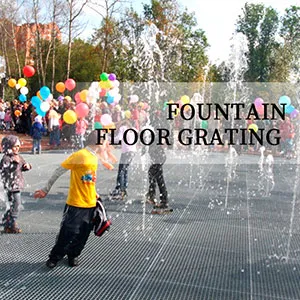
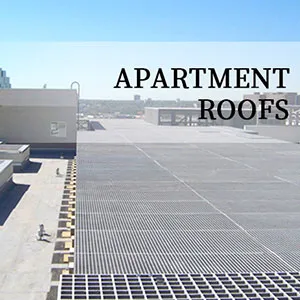
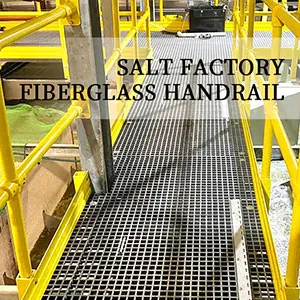
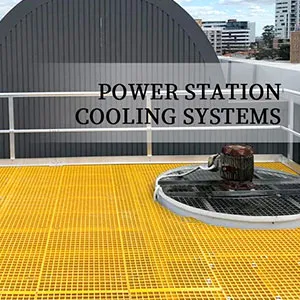
About the Factory
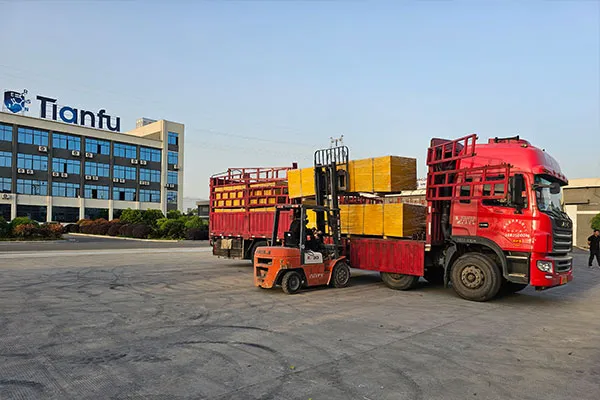
We are a professional FRP Grating manufacturer with 20+ years of experience. Our 26,000㎡ factory is ISO9001 certified, serving clients across 30+ countries with OEM/ODM capability. We provide customized solutions and fast delivery worldwide.

Our FRP gratings are manufactured in accordance with ISO 9001 standards and tested per ASTM E84 (Class 1 fire rating), ASTM D638/D790 for mechanical performance, and comply with BS 476 and EN 13706 standards. Third-party testing available through SGS and TUV upon request.
Exhibition
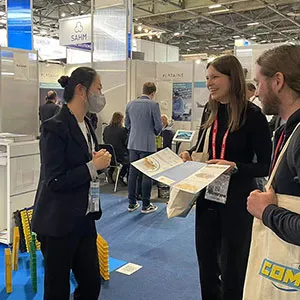
JEC WORLD 2023
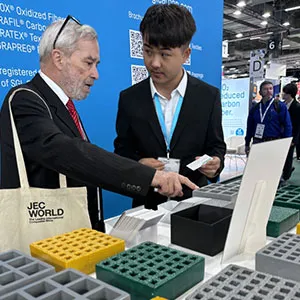
JEC WORLD 2024
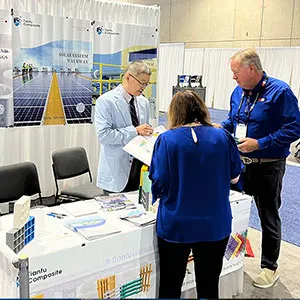
CAMX 2025
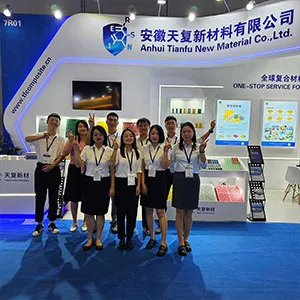
SHANGHAI 2025
Certificate
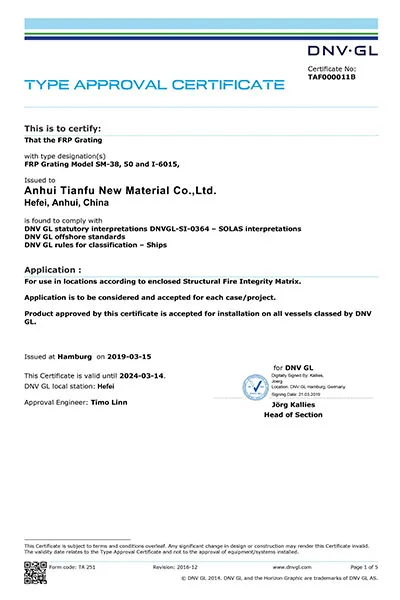
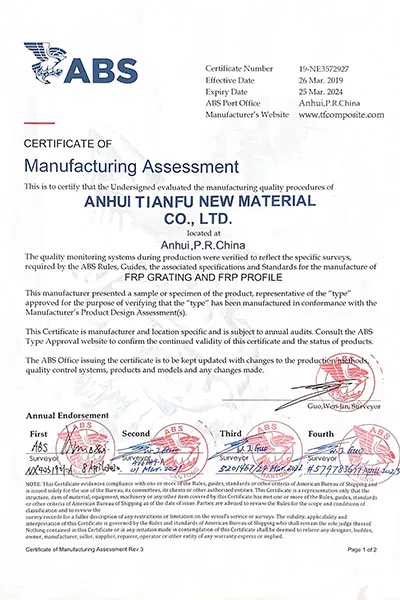
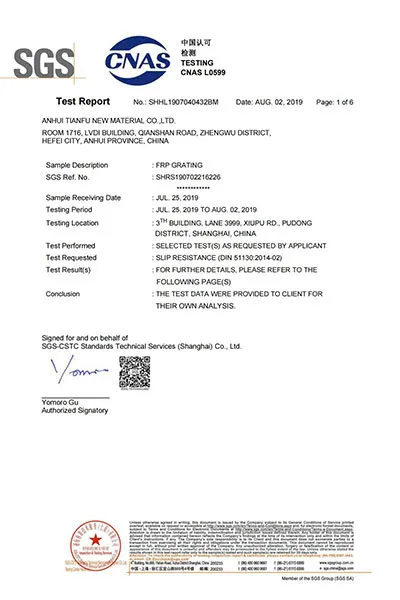
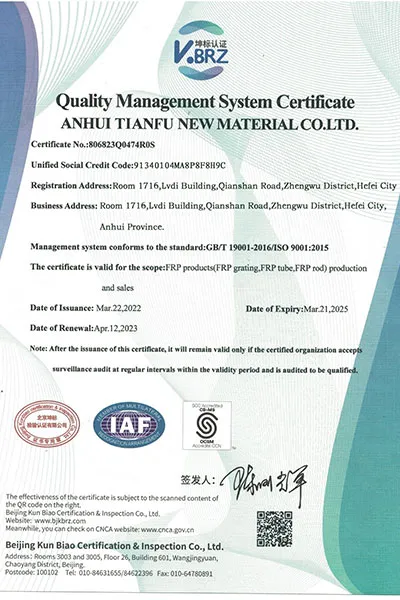
FRP Moulded Grating TDS
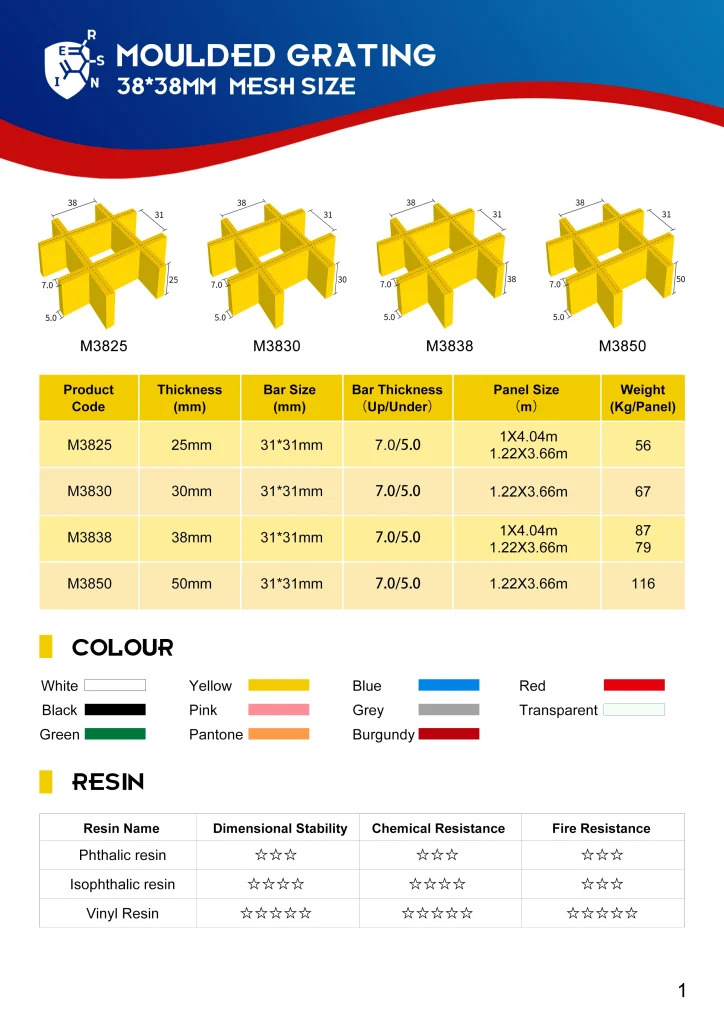
Other Products
VR Factory Tour
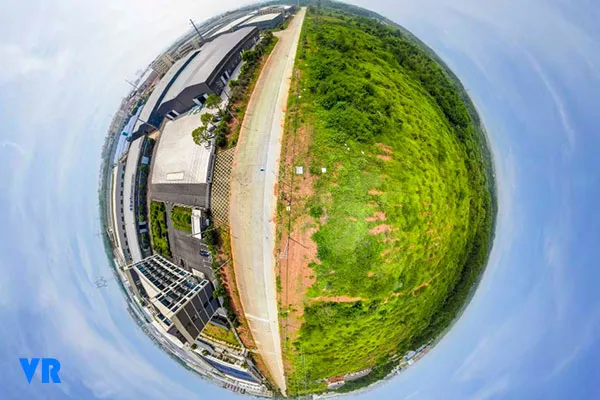
Fiberglass Grating Chemical Plants Power Stations Oil & Gas Refineries Industrial Flooring
Series :
Fiberglass Molded Grating >application
Industrial Flooring,Marine and Offshore Platforms,Wastewater Treatment Plants,Food and Beverage Industry,Transportation Infrastructure,Construction Sites,Battery Rooms and Electrical Substations,Public and Commercial Spaces,Water Parks and Swimming Pools,Rooftop and HVAC Systems
Mesh Size :
38x38 mm (1.5
Thickness (Height) :
25 mm / 30 mm / 38 mm / 50 mm
Panel Size :
1220x3660 mm / 1000x4000 mm / Custom
Open Area :
60% – 70% (depending on mesh size)
Surface Options :
Gritted / Concave / Smooth / Covered Top
Color :
Gray, Yellow, Green, Red, Custom
FAQ
Q :
Why is fiberglass grating preferred for flooring in chemical plants?
A :
Fiberglass grating is highly resistant to corrosive chemicals, acids, and alkalis—making it ideal for the harsh environments found in chemical processing plants. Unlike steel, it does not rust or require painting or galvanizing.
Q :
What types of fiberglass grating are best for chemical plant use?
A :
Molded FRP grating is commonly used due to its excellent corrosion resistance and bi-directional strength. Vinyl ester resin is typically chosen in chemical plant environments because of its superior chemical and heat resistance.
Q :
Is fiberglass grating safe for employees walking in areas exposed to chemicals?
A :
Yes. Most fiberglass grating comes with anti-slip surfaces, such as gritted or concave finishes, to prevent slips even in wet or chemically contaminated areas. Additionally, it’s non-conductive, enhancing safety near electrical equipment.
Q :
How much weight can fiberglass grating support?
A :
Depending on the type and thickness, fiberglass grating can support medium to heavy foot traffic and equipment. Pultruded grating offers higher unidirectional strength, while molded grating provides strength in both directions. Always refer to the load tables provided by the manufacturer.
Q :
Will fiberglass grating degrade in extreme temperatures?
A :
Fiberglass grating performs well across a wide temperature range. With the right resin system (e.g., vinyl ester or phenolic), it can withstand high heat and thermal cycling, common in chemical processing areas.
Q :
How is fiberglass grating maintained in chemical plants?
A :
It requires minimal maintenance. Cleaning can be done using water or non-abrasive cleaners. Since it doesn't rust or peel, there’s no need for repainting or recoating, reducing long-term maintenance costs.
Q :
Can fiberglass grating be customized for complex chemical plant layouts?
A :
Yes. FRP grating is easy to cut and fabricate on-site using standard tools. It’s lightweight and can be quickly shaped to fit around tanks, drains, pipes, and other structures, making installation fast and flexible.
Other related products