Product performance introduction
FRP Pultruded Sections are structural profiles made from Fiber Reinforced Polymer (FRP) using a manufacturing process called pultrusion. This method involves pulling continuous strands of reinforcing fibers (typically glass or carbon) through a resin bath and then through a heated die to form profiles of constant cross-section. The result is a lightweight, high-strength, corrosion-resistant material ideal for a wide range of structural applications.
Common FRP pultruded shapes include I-beams, channels, angles, square tubes, round tubes, flat bars, and custom profiles. These sections are widely used in industries such as construction, chemical processing, electrical, marine, and infrastructure, where traditional materials like steel, aluminum, or wood are prone to corrosion, rot, or electrical conductivity issues.
The key benefits of FRP pultruded sections include:
- Corrosion resistance: Ideal for harsh chemical environments, offshore platforms, or wastewater treatment plants.
- High strength-to-weight ratio: Stronger than steel by weight, yet up to 75% lighter, making transportation and installation easier.
- Electrical insulation: Non-conductive, suitable for high-voltage environments and power plants.
- Durability: Unaffected by UV exposure, saltwater, and most chemicals; minimal maintenance required.
- Design flexibility: Available in a wide range of shapes, sizes, and custom designs.
These profiles comply with international standards such as ASTM D638, ASTM D790, EN 13706, and can be engineered to meet specific load-bearing requirements. They are also fire-retardant and UV-stabilized when needed.
FRP Pultruded Section Specifications & Technical Parameters
Specification | Details / Options |
---|---|
Material Composition | Continuous E-glass (or Carbon/Basalt) fibers + Thermosetting resins (Polyester, Vinyl Ester, Epoxy) |
Manufacturing Process | Pultrusion (continuous pulling through a resin bath and heated die) |
Common Shapes | I-Beam, Channel (C), Angle (L), Square Tube, Round Tube, Flat Bar, T-bar, Custom Profiles |
Standard Sizes | Widths: 25 mm to 300 mm+; Wall thickness: 3 mm to 20 mm+ |
Standard Lengths | 3 m, 6 m, or custom up to 12 m |
Surface Finish | Smooth or textured; resin-rich surface; UV-resistant topcoat (optional) |
Color Options | Grey, Yellow, Green, or Custom |
Fire Resistance | Available with fire-retardant resins (meets ASTM E84, UL 94) |
UV Resistance | Yes, with UV inhibitors or surface veils |
Standards Compliance | ASTM D638, ASTM D790, EN 13706, ISO 527, BS 476, NEMA standards |
FRP Pultruded Section Technical Parameters
Property | Typical Values |
---|---|
Density | 1.6 – 2.0 g/cm³ |
Tensile Strength | 200 – 600 MPa (depending on fiber and direction) |
Flexural Strength | 200 – 500 MPa |
Compressive Strength | 150 – 400 MPa |
Modulus of Elasticity | 8 – 25 GPa (fiber orientation-dependent) |
Impact Strength | Good (Izod: >20 kJ/m²) |
Thermal Conductivity | Low (~0.3 W/m·K) – good insulation |
Electrical Conductivity | Non-conductive (electrically insulating) |
Temperature Range | -40°C to +120°C (up to 180°C with high-temp resins) |
Water Absorption | <0.5% |
Corrosion Resistance | Excellent – resistant to saltwater, acids, alkalis |
UV Resistance | High (with protective coatings or UV-stable resins) |
Why Choose Us
Expertise in FRP Grating Manufacturing
With over 20 years of experience, our factory specializes exclusively in the design, development, and production of high-performance FRP (Fiberglass Reinforced Plastic) gratings. Our deep industry knowledge ensures that every product meets the most demanding industrial standards.
Advanced Technology and Equipment
We utilize state-of-the-art manufacturing equipment and precision molding technology to produce gratings with superior strength, corrosion resistance, and dimensional accuracy. Our commitment to innovation means your project benefits from the latest advancements in FRP technology.
Customized Solutions
From panel sizes and resin types to surface finishes and colors, we offer complete customization to meet your unique application needs—be it industrial flooring, stair treads, trench covers, or marine platforms.
Stringent Quality Control
Every product undergoes a rigorous quality inspection process, including load testing, flame retardance checks, and corrosion resistance analysis. Our ISO-certified quality management system ensures consistent excellence in every batch.
Competitive Pricing
We offer factory-direct pricing without compromising on quality. With optimized production processes and bulk manufacturing capabilities, we help our customers achieve cost savings at scale.
Reliable Delivery and Global Reach
We maintain a large stock of standard products and operate a streamlined logistics system, ensuring fast delivery times locally and internationally. We’ve successfully served clients in over 15 countries.
Hot-Selling Products
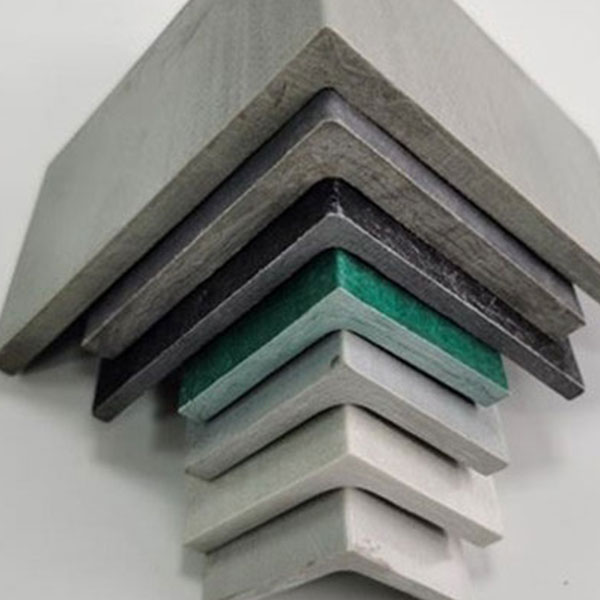
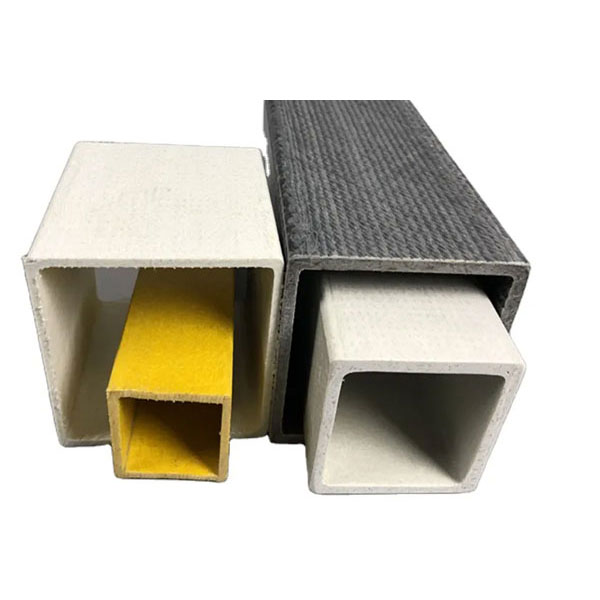
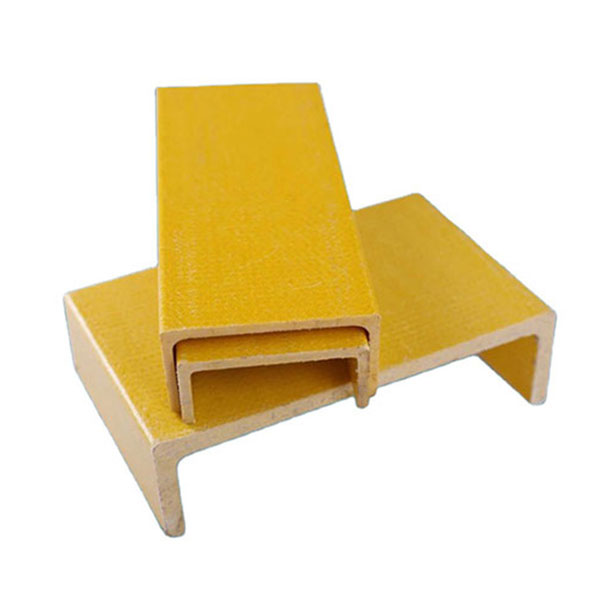
Application Scenarios
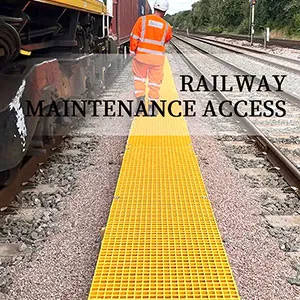
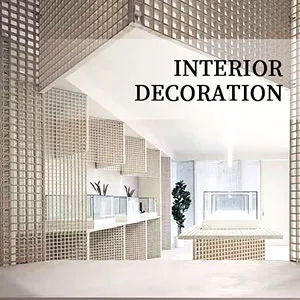
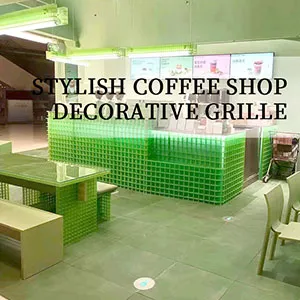
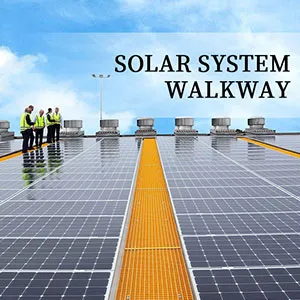
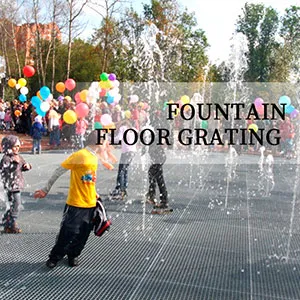
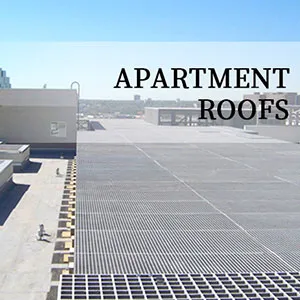
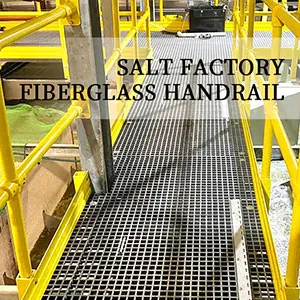
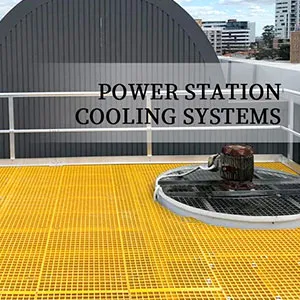
About the Factory
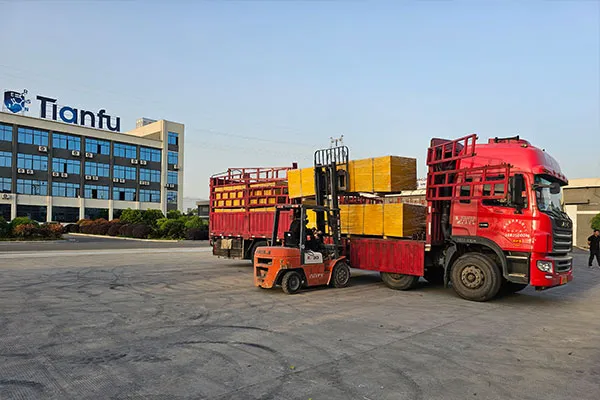
We are a professional FRP Grating manufacturer with 20+ years of experience. Our 26,000㎡ factory is ISO9001 certified, serving clients across 30+ countries with OEM/ODM capability. We provide customized solutions and fast delivery worldwide.

Our FRP gratings are manufactured in accordance with ISO 9001 standards and tested per ASTM E84 (Class 1 fire rating), ASTM D638/D790 for mechanical performance, and comply with BS 476 and EN 13706 standards. Third-party testing available through SGS and TUV upon request.
Exhibition
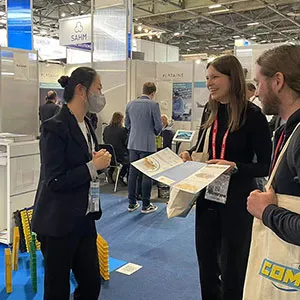
JEC WORLD 2023
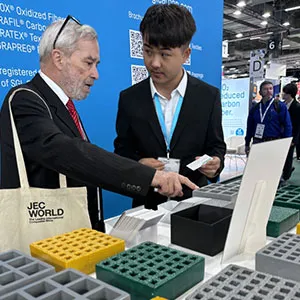
JEC WORLD 2024
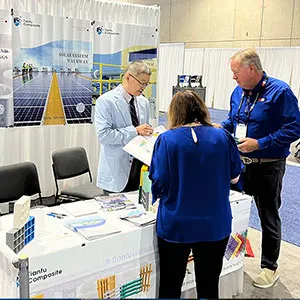
CAMX 2025
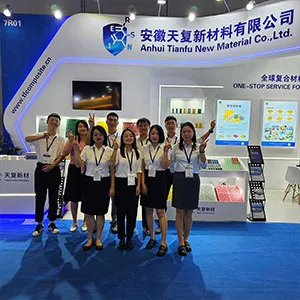
SHANGHAI 2025
Certificate
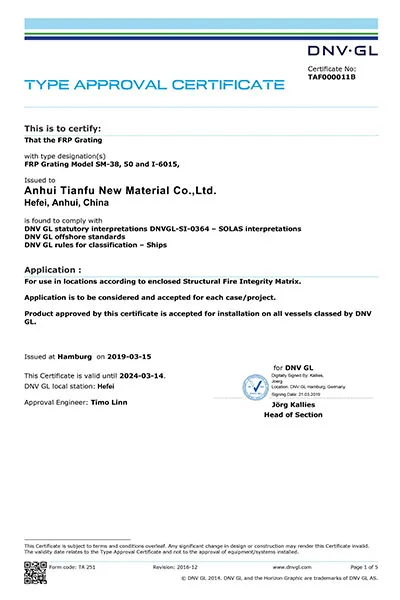
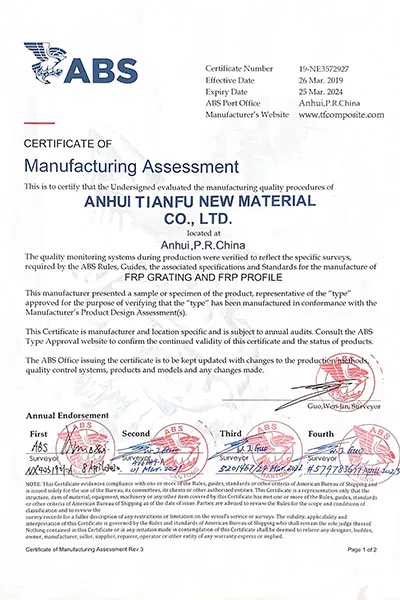
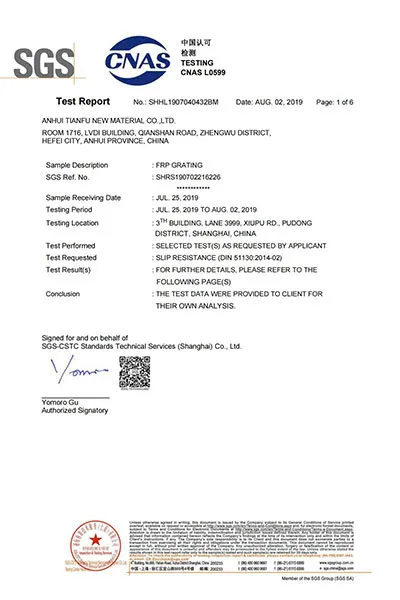
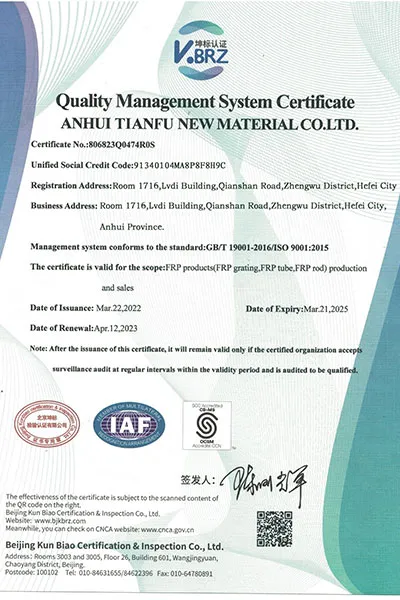
Other Products
VR Factory Tour
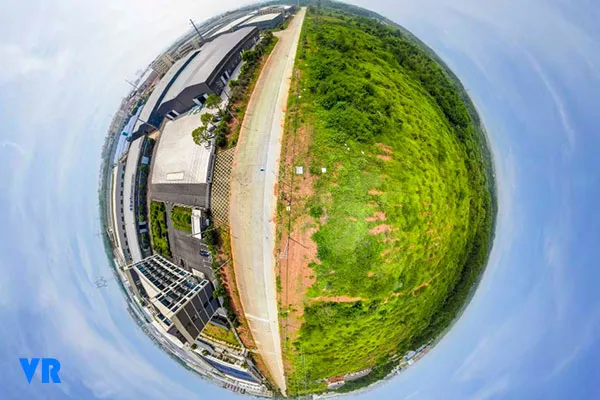
FRP Pultruded Section
Series :
Fiberglass Pultruded Profiles >application
Walkways, handrails, ladders Cooling tower structures Cable trays and supports Chemical processing plants Bridges and offshore platforms Power and utility infrastructure
Material Composition :
Continuous E-glass (or Carbon/Basalt) fibers + Thermosetting resins (Polyester, Vinyl Ester, Epoxy)
Manufacturing Methods :
Pultrusion (continuous pulling through a resin bath and heated die)
Common Shapes :
I-Beam, Channel (C), Angle (L), Square Tube, Round Tube, Flat Bar, T-bar, Custom Profiles
Standard Sizes :
Widths: 25 mm to 300 mm+; Wall thickness: 3 mm to 20 mm+
Standard Lengths :
3 m, 6 m, or custom up to 12 m
Surface Finish :
Smooth or textured; resin-rich surface; UV-resistant topcoat (optional)
FAQ
Q :
What is a pultruded FRP section?
A :
A pultruded FRP section is a structural profile made by pulling continuous fibers (like glass or carbon) through a thermosetting resin bath and a heated die, forming shapes such as I-beams, channels, or angles. The result is a high-strength, corrosion-resistant composite material.
Q :
What shapes are available in FRP pultruded profiles?
A :
I-Beams Channels (C-section) Angles (L-section) Square and Round Tubes Flat Bars T-bars Custom cross-sections on request
Q :
What are the advantages of using FRP pultruded sections?
A :
High strength-to-weight ratio Corrosion and chemical resistance Electrically non-conductive UV and weather resistant Lightweight and easy to install Low maintenance Long service life
Q :
Are FRP pultruded sections fire resistant?
A :
Yes, fire-retardant grades are available using special resins that meet standards such as ASTM E84 or UL 94.
Q :
Can FRP sections be used outdoors?
A :
Yes. With UV-resistant coatings or resin systems, FRP pultruded profiles perform well in outdoor and marine environments.
Q :
How do you connect or join FRP sections?
A :
FRP profiles can be connected using: Bolted joints FRP or stainless steel fasteners Adhesives Mechanical brackets Pre-drilled holes and custom fabrication services are also commonly available.
Q :
Are FRP sections safe to use near electrical equipment?
A :
Yes, they are non-conductive, making them ideal for use near electrical installations or in high-voltage environments.
Q :
What is the typical lifespan of a pultruded FRP profile?
A :
Properly installed FRP sections can last 50+ years, even in harsh industrial or marine environments.
Other related products