Product performance introduction
Fiber Reinforced Polymer (FRP) rebar is a high-performance alternative to traditional steel reinforcement bars used in concrete structures. Made from a combination of fibers such as glass, carbon, or basalt and a polymer resin matrix (usually vinyl ester, polyester, or epoxy), FRP rebar provides superior resistance to corrosion, making it ideal for use in environments where traditional steel reinforcement would deteriorate over time due to exposure to moisture, salt, or chemicals.
One of the most significant advantages of FRP rebar is its non-corrosive nature. In structures such as bridges, marine environments, tunnels, and parking garages, corrosion of steel rebar can lead to spalling, cracking, and overall structural degradation. FRP rebar eliminates this problem, offering a much longer service life and reducing maintenance costs. It is also lightweight—approximately 20% of the weight of steel—which makes transportation, handling, and installation easier and more cost-effective.
FRP rebar also boasts high tensile strength. Although it is not as ductile as steel, FRP can achieve similar structural performance when properly designed. Its electromagnetic neutrality makes it suitable for use in sensitive applications such as MRI rooms or near power transmission lines, where metallic interference would be problematic. Additionally, it does not conduct electricity, enhancing safety in specific installations.
The manufacturing of FRP rebar involves specialized machines designed to combine the fibers and resin into a strong composite bar. FRP rebar production machines are typically automated and involve a pultrusion process. In this process, continuous strands of fiber are pulled through a resin bath, where they are coated and saturated. The saturated fibers are then pulled through a heated die that shapes and cures them into the desired diameter and surface texture of the rebar.
Modern FRP rebar machines are engineered for high efficiency, consistent quality, and scalable output. They can produce rebar in various diameters, surface deformations (for improved bonding with concrete), and lengths. The control systems on these machines allow precise monitoring of speed, temperature, and material ratios to ensure uniform quality. Some advanced systems even integrate quality control mechanisms such as infrared scanners and automatic cutting units for continuous operation.
In recent years, the adoption of FRP rebar and its manufacturing technology has grown significantly due to increasing awareness of sustainable building materials and the rising costs associated with steel corrosion. Governments and infrastructure agencies around the world are incorporating FRP rebar into standards and design codes, paving the way for broader use in civil engineering projects.
The market for FRP rebar and related machinery is expected to grow substantially over the next decade. As the construction industry seeks to meet sustainability goals and reduce lifecycle costs, the demand for durable, non-corrosive reinforcement will continue to rise. Manufacturers of FRP rebar machines are responding with more advanced, automated systems to meet this demand efficiently.
FRP Rebar and Machine Specifications & Technical Parameters
FRP Rebar Specifications
Parameter | Typical Values |
---|---|
Material Composition | Fibers (Glass, Carbon, Basalt) + Polymer Resin (Vinyl Ester, Epoxy, or Polyester) |
Tensile Strength | 600–1,500 MPa (depending on fiber type) |
Modulus of Elasticity | 35–60 GPa |
Density | 1.5–2.0 g/cm³ (approx. 25% of steel’s weight) |
Thermal Expansion Coefficient | 6–12 x 10⁻⁶ /°C (similar to concrete) |
Electrical Conductivity | Non-conductive |
Corrosion Resistance | Excellent – unaffected by chlorides, chemicals |
Standard Diameters | 4 mm to 32 mm (custom sizes available) |
Surface Texture | Sand-coated, Helical ribs, Spiral-wrapped |
Fire Resistance | Moderate (depends on resin; may require coating) |
Water Absorption | < 0.25% |
UV Resistance | High (with protective coating) |
Bond Strength with Concrete | ≥ 15 MPa (with ribbed surface) |
FRP Rebar Machine Specifications
Component | Description/Specification |
---|---|
Process Type | Pultrusion (Continuous Fiber Reinforced Process) |
Production Speed | 0.5 to 2.5 meters per minute (depending on diameter and resin type) |
Power Supply | 380V, 3-phase, 50/60 Hz (adjustable for regional standards) |
Installed Power | 15–30 kW (varies by machine size and output capacity) |
Heating System | Electric or oil heating, temperature range: 100°C to 180°C |
Die Molding Unit | Custom die sets for each diameter; stainless steel for precision forming |
Tension Control System | Adjustable tensioners for continuous fiber feed and pull force |
Resin Bath System | Thermostatically controlled resin tank with agitators |
Cooling System | Water spray or air cooling after die exit |
Cutting Unit | Automatic saw with length programming (±2 mm accuracy) |
Control Panel | PLC-based system with touchscreen HMI for full process control |
Dimensions | 10–20 meters in length (depending on machine configuration) |
Output Range | 4 mm to 32 mm diameter FRP rebar |
Automation Level | Semi-automatic to fully automatic lines available |
Safety Features | Emergency stops, thermal protection, overload sensors |
Why Choose Us
Expertise in FRP Grating Manufacturing
With over 20 years of experience, our factory specializes exclusively in the design, development, and production of high-performance FRP (Fiberglass Reinforced Plastic) gratings. Our deep industry knowledge ensures that every product meets the most demanding industrial standards.
Advanced Technology and Equipment
We utilize state-of-the-art manufacturing equipment and precision molding technology to produce gratings with superior strength, corrosion resistance, and dimensional accuracy. Our commitment to innovation means your project benefits from the latest advancements in FRP technology.
Customized Solutions
From panel sizes and resin types to surface finishes and colors, we offer complete customization to meet your unique application needs—be it industrial flooring, stair treads, trench covers, or marine platforms.
Stringent Quality Control
Every product undergoes a rigorous quality inspection process, including load testing, flame retardance checks, and corrosion resistance analysis. Our ISO-certified quality management system ensures consistent excellence in every batch.
Competitive Pricing
We offer factory-direct pricing without compromising on quality. With optimized production processes and bulk manufacturing capabilities, we help our customers achieve cost savings at scale.
Reliable Delivery and Global Reach
We maintain a large stock of standard products and operate a streamlined logistics system, ensuring fast delivery times locally and internationally. We’ve successfully served clients in over 15 countries.
Hot-Selling Products
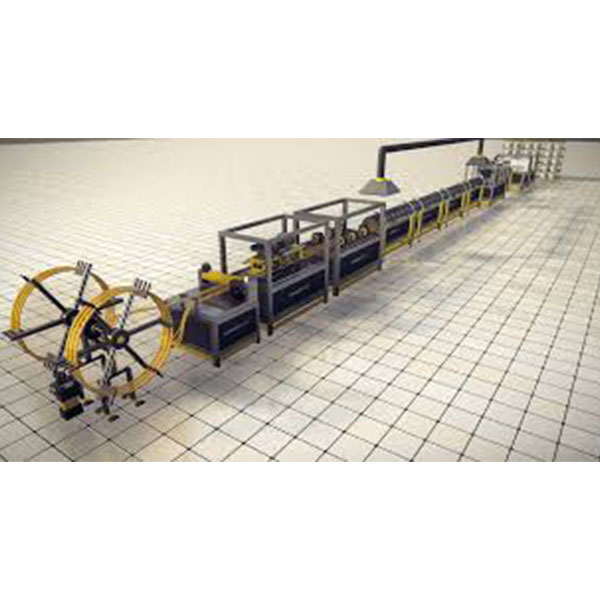
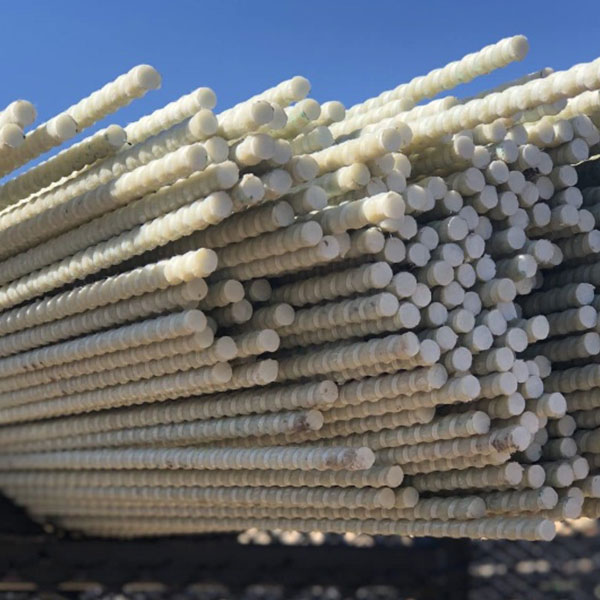
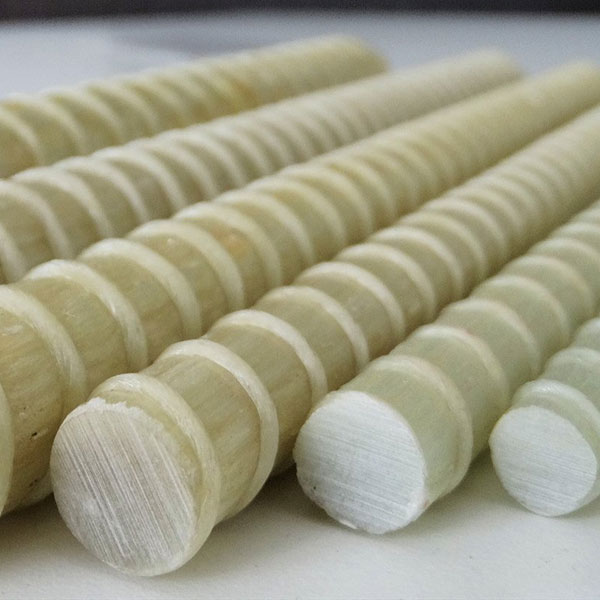
Application Scenarios
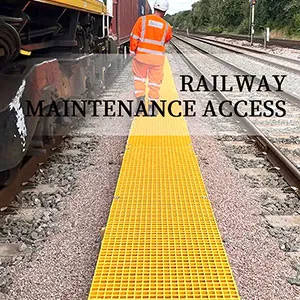
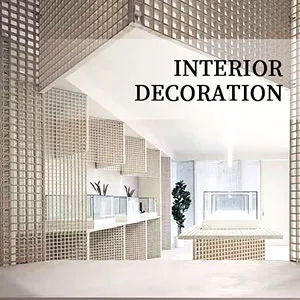
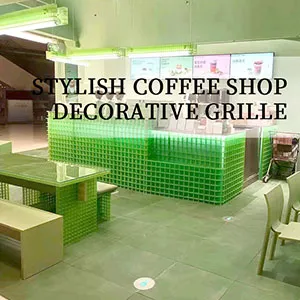
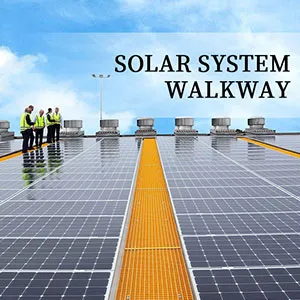
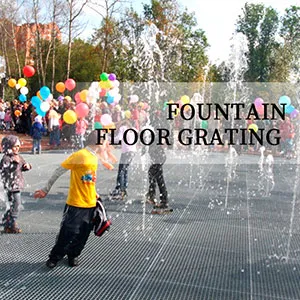
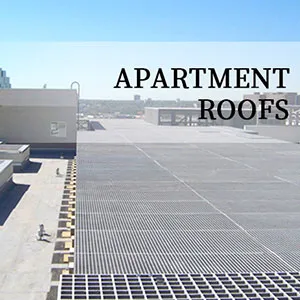
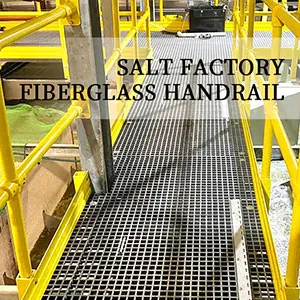
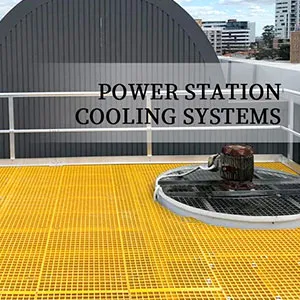
About the Factory
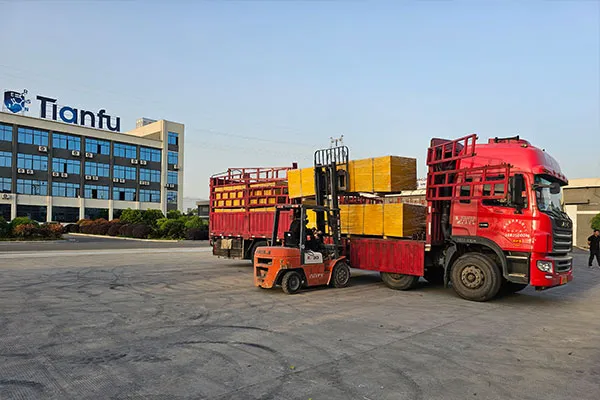
We are a professional FRP Grating manufacturer with 20+ years of experience. Our 26,000㎡ factory is ISO9001 certified, serving clients across 30+ countries with OEM/ODM capability. We provide customized solutions and fast delivery worldwide.

Our FRP gratings are manufactured in accordance with ISO 9001 standards and tested per ASTM E84 (Class 1 fire rating), ASTM D638/D790 for mechanical performance, and comply with BS 476 and EN 13706 standards. Third-party testing available through SGS and TUV upon request.
Exhibition
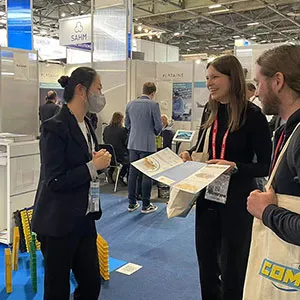
JEC WORLD 2023
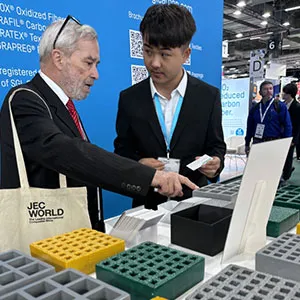
JEC WORLD 2024
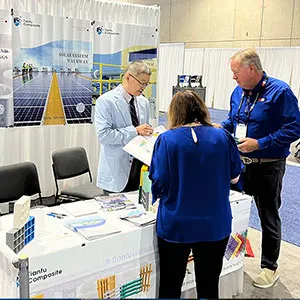
CAMX 2025
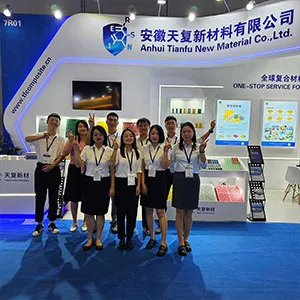
SHANGHAI 2025
Certificate
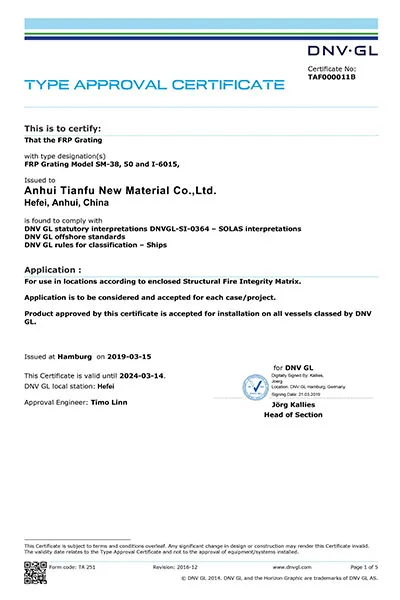
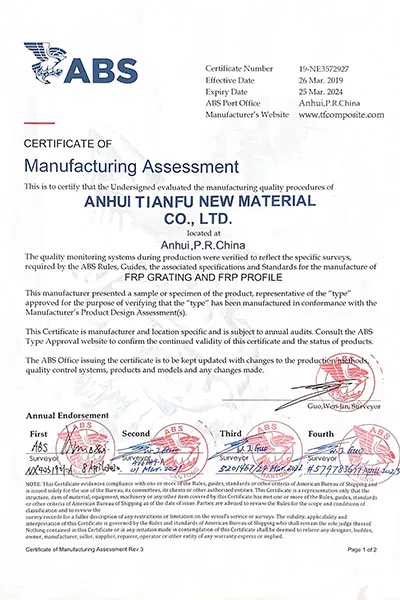
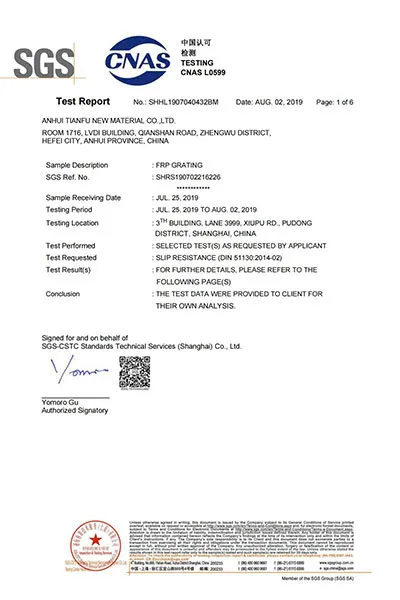
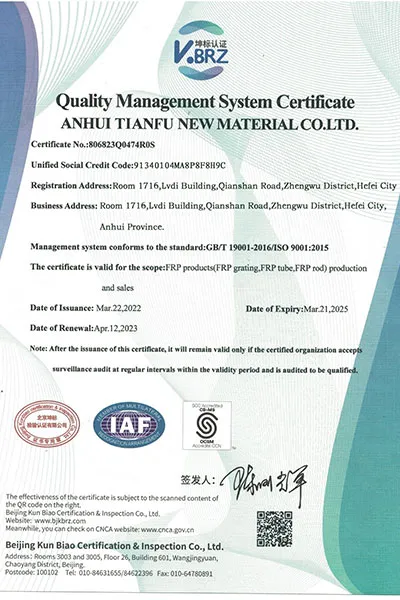
Other Products
VR Factory Tour
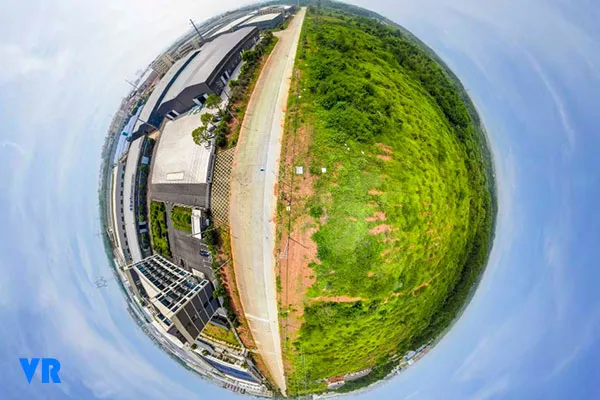
FRP Rebar and Machine
Series :
FRP Rebar And Rebar Machine >application
Bridges and highways Marine structures (ports, docks, seawalls) Tunnels and underground facilities Chemical plants and wastewater facilities Buildings near electromagnetic fields (e.g., hospitals, MRI rooms) Power plants and utilities
Material Composition :
Fibers (Glass, Carbon, Basalt) + Polymer Resin (Vinyl Ester, Epoxy, or Polyester)
Tensile Strength :
600–1,500 MPa (depending on fiber type)
Modulus of Elasticity :
35–60 GPa
Density :
1.5–2.0 g/cm³ (approx. 25% of steel’s weight)
Thermal Expansion Coefficient :
6–12 x 10⁻⁶ /°C (similar to concrete)
Electrical Conductivity :
Non-conductive
FAQ
Q :
Is FRP rebar as strong as steel?
A :
Yes, FRP rebar has higher tensile strength than steel (up to 1,500 MPa), but it has a lower modulus of elasticity, meaning it stretches more under load. It is designed to match or exceed steel's performance in properly engineered structures.
Q :
Can FRP rebar be bent on-site?
A :
No. Unlike steel, FRP rebar cannot be bent after manufacturing. All bends or shapes must be pre-formed in the factory to required specifications.
Q :
Is FRP rebar approved in building codes?
A :
Yes. Many countries now include FRP rebar in their design standards and building codes, such as ACI 440.1R in the U.S. and CSA S806 in Canada. Approval depends on local regulations and project specifications.
Q :
Does FRP rebar bond well with concrete?
A :
Yes. FRP rebar is manufactured with surface treatments (e.g., sand-coating, helical wraps) to enhance bonding with concrete, achieving bond strengths similar to or better than steel.
Q :
What is the lifespan of FRP rebar?
A :
FRP rebar can last over 100 years in harsh environments due to its corrosion-resistant properties, significantly outperforming steel in high-moisture or chemically aggressive settings.
Q :
Is FRP rebar more expensive than steel?
A :
Initial cost of FRP rebar is typically higher, but the lifecycle cost is lower due to reduced maintenance, longer lifespan, and corrosion resistance.
Q :
Can FRP rebar be recycled?
A :
FRP rebar is not recyclable in the same way as steel, but it can be reused in some cases and disposed of as non-hazardous waste. Some research is being done into composite recycling techniques.
Other related products